La industria química, caracterizada por sus procesos intrincados y demandas precisas, se apoya en la eficiencia de sus sistemas para prosperar. En este contexto, las válvulas industriales en la industria química desempeñan un papel fundamental, actuando como componentes esenciales en el control del flujo y la gestión de procesos. En este extenso artículo, exploraremos en detalle la importancia, la variedad, y las innovaciones relacionadas con las válvulas industriales en el contexto específico de la industria química.
Variedad de Tipos de Válvulas para Adaptarse a Cada Necesidad
En el corazón de la optimización de procesos químicos se encuentran las distintas categorías de válvulas industriales. Desde las versátiles válvulas de bola que proporcionan un control preciso del flujo, hasta las robustas válvulas de compuerta que se destacan en aplicaciones de cierre hermético, la industria química requiere una gama diversa de soluciones. Las válvulas de globo encuentran su utilidad en la regulación fina del flujo, mientras que las válvulas de mariposa ofrecen una opción eficiente para el control de grandes volúmenes de fluido.
La variedad de tipos de válvulas permite a las empresas en la industria química adaptar sus sistemas a las necesidades específicas de cada proceso. Cada tipo de válvula tiene sus propias características únicas, lo que permite una selección precisa y personalizada según los requisitos de operación.
Selección de Materiales para Resistencia a la Corrosión y Productos Químicos Agresivos
La resistencia a la corrosión es un requisito imperativo en la industria química, donde los componentes están constantemente expuestos a productos químicos agresivos. Aquí es donde la elección de materiales adecuados se convierte en un factor crítico. Las válvulas industriales de alta calidad se construyen utilizando materiales avanzados que ofrecen resistencia excepcional a la corrosión.
Materiales como acero inoxidable, aleaciones de níquel y revestimientos especiales proporcionan una barrera efectiva contra la corrosión. La durabilidad y la longevidad de estas válvulas están directamente relacionadas con la calidad de los materiales utilizados en su construcción.
Adherencia a Rigurosas Normativas y Estándares de Calidad
La seguridad es una prioridad en la manipulación de productos químicos, y las válvulas industriales deben cumplir con normativas y estándares rigurosos para garantizar un rendimiento seguro y confiable. Organismos de normalización y certificación establecen pautas específicas para la fabricación y el funcionamiento de las válvulas en entornos químicos.
Las normativas y estándares abordan aspectos como la resistencia a la presión, la capacidad de estanquedidad, y la durabilidad de las válvulas. La adherencia a estos estándares asegura que las válvulas cumplan con los requisitos esenciales para su aplicación en la industria química.
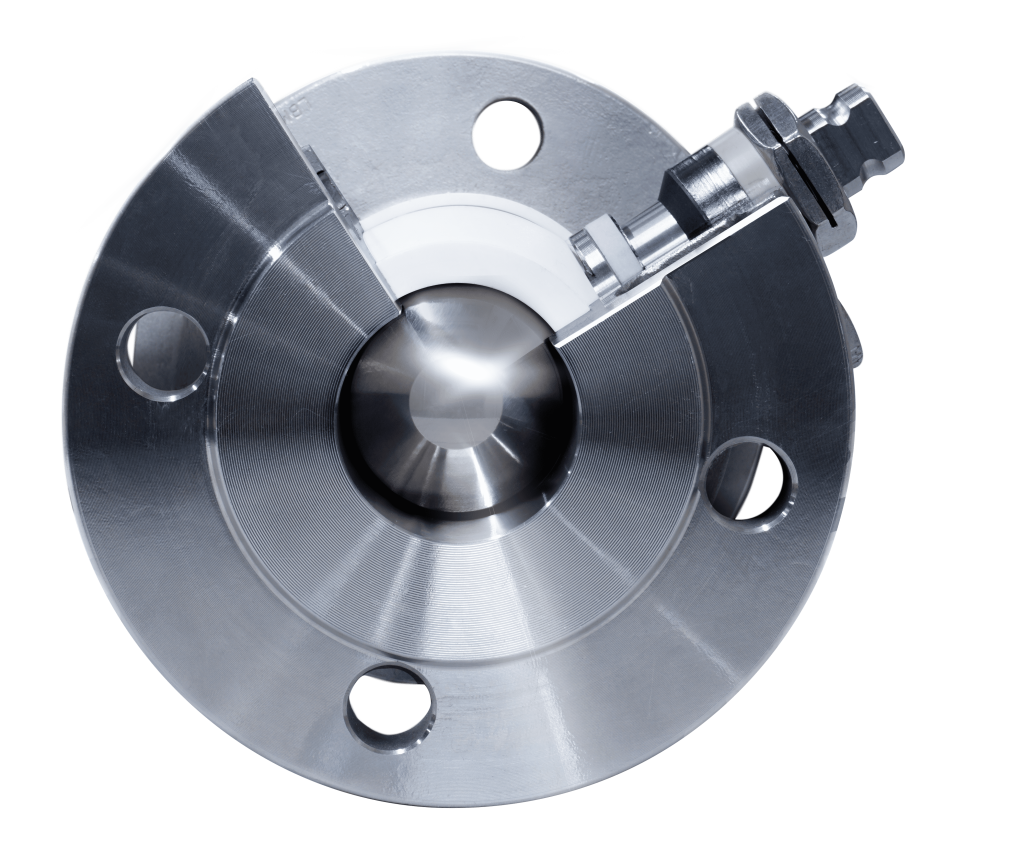
Automatización y Control para Optimización de Procesos
La automatización de procesos ha revolucionado la eficiencia en la industria química, y las válvulas automatizadas desempeñan un papel clave en este avance. La capacidad de controlar el flujo de manera precisa y rápida contribuye a la optimización de los procesos, mejorando la eficiencia operativa y reduciendo los riesgos asociados con la manipulación manual.
La integración de sistemas de control avanzados permite monitorear y ajustar las válvulas de manera remota, adaptándolas a las variaciones en las condiciones del proceso. Esto no solo mejora la eficiencia, sino que también reduce la posibilidad de errores humanos.
Innovaciones Tecnológicas para Desafíos Específicos
La constante búsqueda de mejoras ha llevado a innovaciones tecnológicas significativas en el diseño de válvulas industriales. Las empresas líderes en el sector estamos incorporando características inteligentes en nuestros productos para abordar desafíos específicos. Sensores de monitoreo en tiempo real, sistemas de autodiagnóstico y tecnologías de sellado avanzadas son ejemplos de innovaciones que mejoran la confiabilidad y la seguridad de las válvulas en entornos químicos.
La investigación y desarrollo continuo en el campo de las válvulas industriales busca soluciones a desafíos particulares, como la variabilidad química y las condiciones extremas de operación. Estas innovaciones no solo mejoran el rendimiento de las válvulas, sino que también contribuyen a la eficiencia general de los procesos en la industria química.
Sostenibilidad y Contribución Ambiental
La sostenibilidad es un tema central en todas las industrias en la actualidad, y la industria química no es una excepción. Las válvulas industriales que incorporan prácticas sostenibles y materiales ecoamigables están ganando relevancia. La eficiencia energética en la operación de las válvulas, la reducción de emisiones y el uso de materiales reciclables son aspectos clave de esta tendencia hacia la sostenibilidad.
La contribución ambiental de las válvulas industriales va más allá de su funcionamiento en procesos químicos; se extiende a las prácticas de fabricación y la gestión de residuos. Las empresas líderes reconocen la importancia de este enfoque integral hacia la sostenibilidad.
Superación de Desafíos Comunes en la Industria Química
La industria química presenta desafíos únicos que las válvulas industriales de calidad están diseñadas para superar. La corrosión, resultado de la interacción constante con productos químicos agresivos, es uno de estos desafíos. Las válvulas de alta calidad emplean tecnologías y materiales resistentes a la corrosión para garantizar una larga vida útil y un rendimiento confiable.
La variabilidad química, donde la composición de los productos puede cambiar, también es abordada por válvulas diseñadas para adaptarse a diferentes condiciones.Además, las válvulas resistentes a la abrasión encuentran su aplicación en entornos donde los fluidos.
Desafíos Comunes y Soluciones de FHT Valves
Corrosión, abrasión y variabilidad química son desafíos comunes. Descubra cómo las válvulas de FHT Valves superan estos desafíos, ofreciendo soluciones robustas y duraderas para mantener la integridad de los sistemas en entornos químicos exigentes.
Miramos hacia el futuro de la tecnología de válvulas en la industria química y cómo FHT Valves anticipa y se adapta a las demandas cambiantes del sector. Nuestra visión es seguir siendo líderes en ofrecer soluciones innovadoras y sostenibles para la industria química.
Con una amplia gama de productos y un compromiso constante con la excelencia, las válvulas de FHT Valves son la elección preferida para empresas que buscan optimizar sus operaciones en la industria química, como las válvulas de fondo de cuba, asientos integrales o con asientos metálicos.